Innovation can take many forms, and these can include making existing technology work better and more efficiently. Swirltex is committed to doing exactly that. The company produces custom, modular wastewater treatment systems that use buoyancy-based membrane filtration to more efficiently separate solids and liquids, producing higher-quality effluent and better production rates while requiring less energy. Swirltex’s technology is designed to augment existing wastewater infrastructure, eliminating the need for expensive capital upgrades. In this interview, Swirltex CEO Melanie McClare tells Municipal Water Leader about how Swirltex is driving innovation across the wastewater management sector.
Municipal Water Leader: Please tell us about your background and how you came to be in your current position.
Melanie McClare: I have a chemical engineering background. Right out of school, I bounced around the world to countries in Europe and West Africa, mainly in the industrial sector. I landed in the water industry in 2008, when I started working for a fast-growing company called FilterBoxx that serviced customers through a fully containerized modular approach to solving water and wastewater problems. Most of the sales happened in Canada. During my 9 years at FilterBoxx, I started working on my MBA. One of the programs that was part of the MBA was an accelerator for deep science–based technology companies that needed business help. That’s how I met the founder of Swirltex, Peter Christou. He had invented this wastewater technology in his garage and had had the opportunity to test it in Antarctica for the European Space Agency. I thought that was a really interesting start to his journey. I was fascinated by the technology, and he needed some help on the business side getting the company going and raising capital. I took the leap and joined Peter in 2018. Since then, we’ve grown the company, and we are now servicing three different vertical markets. We have some amazing customers, and it’s been an awesome 3 years.
Municipal Water Leader: Tell us about Swirltex as a company.
Melanie McClare: We’re a team of nine headquartered in Calgary, Alberta, Canada; we have a few people in Houston, Texas, as well. We serve both industrial and municipal customers and target wastewater reuse. We currently operate in Canada and the United States. We’re focusing on growing into the South American and Asia-Pacific markets over the next 2 years.
Municipal Water Leader: What was the problem that you aimed to solve with your new technology?
Melanie McClare: The original problem was membrane fouling. That is a technical problem that means that you can’t always use membranes on difficult wastewater streams. Our solution allows membranes to operate on tougher wastewater streams than they have been able to in the past.
Our business model also responds to the fact that some customers only need their infrastructure polished or upgraded temporarily or seasonally. We offer a pay-for-performance business model according to which we bring a modular asset to the customer’s facility where and when they need it. That means that they don’t have to invest in a capital infrastructure upgrade to their system. So another problem we are solving is allowing this slow-moving, risk-averse sector to pay for performance and derisk projects for a fraction of the cost of capital upgrades.
Municipal Water Leader: How does your technology work?
Melanie McClare: We use fluid mechanics to make membranes work better. What we do is simple. We inject a gas into the influent stream at a specific volume, bubble size, and flow rate. We then spin the multiphase wastewater through a tubular membrane. The net effect of spinning the water through the tubular membrane is that you get more for less. You can use fewer membranes to achieve the same treated water flow rate, which means that your membranes are performing better and you’re also using significantly less energy per gallon. That is really important in this space, especially for the trickier wastewater streams, high solids loading, or oily streams. Energy is becoming a bigger factor in decisionmaking. We don’t alter the membrane material itself; we play with the fluid mechanics to make existing membranes work better.
Municipal Water Leader: Where does your technology fit in in process terms?
Melanie McClare: Our technology is a polishing step. Our ideal customers are those who have plants and a pinch point within their processes where we can augment their existing infrastructure with our compact membrane system. We are a filtration step, which is a great fit for augmenting existing infrastructure. A side benefit is the gas that we inject, which can augment the biological treatment process at many of our customer sites.
Municipal Water Leader: What size and length are the tubular membranes your system uses?
Melanie McClare: The geometry of the membrane we select will depend on the wastewater. Each tubular membrane module is composed of a bundle of tubes, say a 10‑inch head with 600 tubes in a bundle. We buy off-the-shelf membranes rather than creating them ourselves. We buy tried-and-true, 40‑year-old technology and make it work better.
Municipal Water Leader: What are the membranes typically made of?
Melanie McClare: We mainly use a polymeric membrane. The component that we typically operate with is polyvinylidene difluoride. For particularly high temperature applications, we use other types.
Municipal Water Leader: What is the most energy-intensive element of this process?
Melanie McClare: The pumping. The way that we help customers save energy is by optimizing fluid characteristics within the tube. Basically, we use the wasted space in the tube to benefit the customer by channeling gas and solids toward the center of the tube, away from the membrane surface. That means you can buy much smaller pumps to achieve the same flow rate of treated water.
Municipal Water Leader: What happens to the effluent streams after they go through the tubular membrane?
Melanie McClare: We operate cross-flow filtration, which means that the clean water is squeezed through the membrane and the waste stream continues on through the tube. The waste stream is hyperoxygenated. We return it to the biological pretreatment tank in the case of a municipal application or to the pond in the case of a municipal or industrial pond application. Then, we continually recirculate it back through the membrane system.
Municipal Water Leader: Would you tell us more about how your solution works with pond applications?
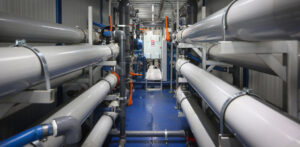
Melanie McClare: Municipal lagoons and ponds are commonly used to manage wastewater in areas like North Dakota. These ponds are expensive to upgrade. Lagoon operators and smaller municipalities that have issues meeting regulatory criteria can benefit from our modular infrastructure.
Municipal Water Leader: What do your clients do with the purified water?
Melanie McClare: All our customers to date have been reusing this water. It’s ultrafiltered, which means that even very small particles, smaller than bacteria, have been removed. Customers can use that ultrafiltered permeate or effluent stream within their processes or to offset water use for things like irrigation.
Municipal Water Leader: Could this water be used immediately for potable purposes, or does it require further treatment?
Melanie McClare: Technically speaking, ultrafiltration can get the water clean enough that, after it is disinfected, it could be used as potable water. Whether that is allowed depends on regulations. It is not very common in North America, although there are states and cities, like San Francisco, that are working on potable reuse applications. None of our current customers are treating the water all the way to the potable level; they’re using it for industrial reuse purposes or in the municipal setting for irrigation and agriculture.
Municipal Water Leader: You alluded earlier to your colleague’s work with the European Space Agency. Is the agency interested in reusing water in space?
Melanie McClare: Yes. For nonearth applications, like the ones we tested in Antarctica, every single drop needs to be recycled.
Municipal Water Leader: Does your product have to be configured differently for industrial and municipal customers?
Melanie McClare: The short answer is no on the membrane side. The way that we design our Swirltex ultrafiltration packaged systems is transferable across multiple verticals. Often, our customers want us to take on pretreatment and provide a full solution, and in certain industrial and municipal segments, the pretreatment for the membrane system will change. While pretreatment can vary from customer to customer, the actual Swirltex piece is the same.
Municipal Water Leader: What is the benefit of your customized, modular product and business model?
Melanie McClare: The more customers we talk to, the more we recognize the importance of decentralizing wastewater infrastructure. Servicing customers in a unique way is becoming more mainstream. The traditional model of municipal wastewater infrastructure sales is changing, and we’re part of that change. Now more than ever, customers can be creative with their solutions because of the flexible offerings of companies like ours.
Municipal Water Leader: What is your company’s vision for the future?
Melanie McClare: Our broad vision is net zero wasted water. We are helping customers and facility owners augment what they have already invested in. We’re not encouraging them to replace old equipment; we’re helping augment what they already have. We allow these facility owners to make smart decisions that benefit their stakeholders faster at a lower cost. Our vision is to help customers get creative and not feel pigeonholed in the traditional wastewater business model.