The evolution of robotics is continually opening more places for exploration, research, and productivity. These can include places that would be dangerous for people to interact with in person, but that robots can reach while controlled from a safe distance. Robots can collect accurate scientific or engineering data, repair or modify existing systems, and even install new equipment safely and efficiently. Copperstone Technologies is leading the way in finding more applications for robots in mining, wastewater, and other industries. In this interview, Craig Milne, Copperstone Technologies’ CEO, tells Municipal Water Leader about how robots increase safety while improving data accuracy, the technologies that make the company’s robots unique, and future applications for robotics in the water industry.
Municipal Water Leader: Please tell us about your background and how you came to be in your current position.
Craig Milne: I’m a scientist by training, with a degree in medical sciences and a degree in finance. I’m a curious person, and I have been involved in lots of different things in my life. For the last 15 years or so, I’ve been involved in a number of technology ventures, a lot of which related to water in one way or another. About 2 years ago, I joined Copperstone. The company was founded by a couple of mechanical engineers from the University of Alberta. While completing their graduate studies, they helped some Canadian mining companies do measurements called tailings in their waste facilities. Copperstone’s founders realized that simply accessing these facilities posed a challenge; they could do the measurements, but they couldn’t get to the actual place where the measurement had to be done. They came up with the concept of an all-terrain vehicle robot that could crawl into a hazardous location, such as a mining waste facility, to take measurements. That’s how Copperstone got started. They operated for a couple of years building some prototypes, and I joined them in January 2019 with the intention of growing the company into a bigger commercial enterprise. Since then, we’ve focused on building commercial-grade robots and working with mining companies to provide them the information they need. We’ve settled on a business model of robots-as-a-service. One of the things we recognized was that not everybody wants to purchase a robot, because it seems like a big investment and a complicated device. It made more sense to employ a business model based on understanding the client’s needs and then either using the robots we have or customizing one as needed. Then we send out a field team that has all the necessary safety training and certifications and collect the data on behalf of the client.
Municipal Water Leader: Would you describe the robot?
Craig Milne: What makes our robot distinctive is that it’s amphibious: it can float in water and drive across the hard ground. There really aren’t a lot of choices when you are looking for an amphibious robot. Our robot can operate anywhere where water and land intersect, including beaches, rivers, canals, utility ditches, ponds, and water storage facilities. The robot has a large pontoon, which allows it to float in water. The pontoon has a helical screw that rotates to serve as a propeller in water or a wheel on hard ground. It also has four-wheel drive. It works quite effectively in transitional zones that have traditionally been difficult for tracked vehicles and wheeled robots to traverse, such as swamps and snow.
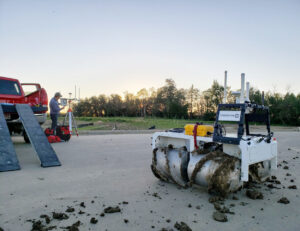
Municipal Water Leader: Does the robot come in different sizes?
Craig Milne: Right now, we have two different sizes. One of them is about 4 feet by 4 feet and weighs a couple hundred pounds. The other one is about 12 feet long, around the size of a small car, and weighs almost 2,000 pounds. We’re looking at going in both directions—building smaller units that are better at crawling through restricted spaces like tunnels as well as bigger units that can carry a lot of mass, since for some of the jobs we do, the robot has to carry a lot of heavy equipment.
Municipal Water Leader: How much do the robots cost?
Craig Milne: They are quite expensive to build, especially as they increase in size. That said, our services eliminate the need for our clients to put four or five people and existing equipment in a hazardous location, which is also quite expensive. We typically charge day rates or project fees. The rates we charge are often cheaper than alternatives that require putting onsite personnel at risk.
Municipal Water Leader: In addition to day rates and project fees, do you have long-term contracts for this service?
Craig Milne: Yes, that’s where we’d like to end up. A long-term contract would make sense for someone who needs to routinely perform maintenance on or inspections of a hazardous permanent facility. We have an autopilot system on the robot, so it can drive a predetermined course using GPS. Some navigation systems are on board, and the rest is controlled remotely.
It sends all its data and video back to a remote base station so that an operator can see what’s happening. We’re also working on even going one step further than that by allowing the information to be sent to an office that is thousands of miles from the robot. It would be like a Mars exploration robot, beaming data back to headquarters, and able to be controlled and seen from headquarters.
Municipal Water Leader: Could this robot be used in an underground water conveyance pipe or sewage pipe?
Craig Milne: That is of high interest, and we are looking at adjusting our design to fit that type of environment. We have been in touch with a European agency about building a robot that would work like that. There are lots of old sewer systems in Europe, many of which have been through wars or bombing events and have interesting histories. If you have a small-diameter pipe, it’s easy to flush it with water, clean it, and then send a tiny crawler down it. We’re finding opportunities with tunnels that are larger, maybe 10 feet wide. You can’t easily clean a 10‑foot-wide tunnel by flushing it with high-pressure water. You actually have to send people or tiny excavators. There is an advantage to sending a robot into unknown spaces like those with hundreds of years of sewage and bricks.
Municipal Water Leader: Can the robot be deployed in a river?
Craig Milne: We haven’t done a lot of river testing, but the robots’ maximum speed is just over 1 meter per second. If the current is much faster than that, we wouldn’t be able to hold a position. We are working on a new robot that has a higher top speed.
The robots also do well in long beaches or debris-laden water, which boats don’t do well with. We’ve also successfully driven the robots through vegetation without damaging them or the vegetation; weeds that would normally get caught in a propeller are not typically a problem because of the pontoons we use.
Municipal Water Leader: Tailing sampling is a mining application, correct?
Craig Milne: It is, but in some ways it’s the same as what happens in environmental sampling.
If you need to know what the bed of a lake or a river looks like, we can take a sampler, drop it to the bottom, and pull up some of the mud. We can take water samples at the surface. We can drop water profiling sensors through the column to understand the temperature, turbidity, and salinity through the entire water column.
Municipal Water Leader: Does your company do data analysis as well?
Craig Milne: We collect the data and samples and provide all the reporting, but we don’t do the interpretation. There are environmental and civil engineers who focus on that side of things; we help them by giving them the full picture of the data.
Municipal Water Leader: What advantages does this system have over conventional methods?
Craig Milne: There are basically two ways of doing this today. The most common method is using people: You might send people out in a boat. There are issues with this approach. Boats can’t traffic in shallow-water areas, and they sometimes get stuck. Putting people in hazardous locations also complicates things. If you have two people in a boat, you also need a safety crew on shore in case there’s a problem. It may take several days of planning to make sure that there are rescue operations, that everyone has life jackets, and that you have the special certifications to be operating on the water. Our system can avoid all of that. Our people stay safe in a warm pickup truck.
Another advantage is precision. With the robot, everything is GPS controlled. We can do a survey every week for a whole summer and take measurements at the exact same survey points with centimeter-level accuracy.
Our robots also have advantages over small robotic or remote-control boats with sensors, which are a competing option. One reason is that the boats can only carry a limited weight. Our larger robots are big enough to carry about 600 pounds. They’re fairly sizable machines that can carry lots of tools.
Municipal Water Leader: Are the robots battery powered?
Craig Milne: They’re all electrical right now. They have rechargeable batteries, and we keep a spare set on shore. The robots can maintain near-continuous operation. When the batteries get low, the robots come home, we swap the batteries out for new ones, and we send them back out. We can recharge the first set of batteries while the robot is still operating.
Municipal Water Leader: So the robot is smart enough to navigate its way home whenever it is running low on battery?
Craig Milne: Yes; we built in a lot of fail-safes like that. Even if one of the robots gets out of radio range and loses communication, it will go back home or return to the last place it had communication to find a new signal.
Municipal Water Leader: How long does a battery charge last?
Craig Milne: Several hours. It depends on what the robot does, weather conditions, and other factors. The robots are as large as they are in part so that they can carry a fairly heavy set of batteries. The more they’re out in the field, the more efficiently our time is being used.
Municipal Water Leader: How do the robots react to adverse weather conditions like rain?
Craig Milne: We do extreme weather tests as much as we can. We’re in northern Canada, so they’ve definitely been cold tested. We’ve operated in thunderstorms during which you can’t put people on the water for safety reasons.
Municipal Water Leader: Is your company active internationally?
Craig Milne: If it weren’t for COVID‑19, we would be. We are global and had to be right from the beginning. There are not a lot of options in northern Canada, where we are based. There’s definitely a strong mining community, and we work with local mining companies. But we also have international collaborations, including a good partnership in Brazil. We’ve had lots of conversations in Australia, but we haven’t started operations there yet. And of course, the United States is just a stone’s throw away.
Municipal Water Leader: What are your other top issues today?
Craig Milne: Awareness, because we’re fairly new. People don’t know that our solution exists. A lot of measurements and monitoring happen in and around water all the time. Sometimes it’s as easy as putting on a pair of hip waders and going out with a bucket, but sometimes it’s really complicated. If people know that there is an alternative, I think they will use it. There are a lot of efficiencies to be gained with robotics, and safety is really important, particularly for a lot of big industrial players. We can offer that in a way that has never been offered before.
Municipal Water Leader: What is your vision for the future?
Craig Milne: We look to things like the Mars exploration that’s happening right now for inspiration. It is a complicated project to send a robot to Mars, but NASA did it because it’s actually simpler and safer than sending people, and the robot is capable of doing all sorts of amazing measurements and exploration. That’s what we want to do here on Earth: to send robots into places that are just too dangerous for people and to do it in a way that is more efficient than the alternatives. We can operate in all weather, during any season, 24 hours a day. Imagine the new data we can easily and safely collect and the benefits that can provide users!
Craig Milne is the CEO of Copperstone Technologies. He can be reached at info@copperstonetech.com.