The Metropolitan Water District of Southern California is a cooperative public agency that provides water to 26 member agencies that serve about 19 million people across a densely populated 5,200‑square-mile service area in Southern California. Its facilities include some of the largest treatment plants in the country, reservoirs, hundreds of miles of large pipeline, and several hydroelectric plants. It also operates the Colorado River Aqueduct, which brings water from Lake Havasu on the California-Arizona border over 240 miles to western Riverside County. Operating and maintaining these immense facilities have inherent hazards associated with them, and to ensure that Metropolitan’s employees stay safe and healthy, the agency has a well-developed operational safety program.
In this interview, Mickey Chaudhuri, Metropolitan’s assistant chief of operations, and Dan Guillory, the section manager for operational safety and regulatory services, tell Municipal Water Leader about how the agency proactively and cooperatively works with its employees to maintain a high standard of safety.
Municipal Water Leader: Please tell us about your backgrounds and how you came to be in your current positions.
Dan Guillory: I’m a senior water industry manager with over 30 years of experience in developing and managing programs in the water industry, specifically in the environmental health and safety field. I’m currently responsible for corporate-wide management of environmental health and safety at Metropolitan. Prior to coming to Metropolitan, I was a consulting engineer, responsible for remediating contaminated properties throughout the western United States. I’ve been involved in developing, designing, and managing Metropolitan’s environmental and safety programs for about 30 years, and my position today is section manager for operational safety and regulatory services.
Mickey Chaudhuri: I have about 24 years in the water and environmental field and am currently the assistant chief of operations at Metropolitan. Our Water System Operations Group consists of about 950 employees, which is about half the agency’s total workforce. We’re responsible for operating and maintaining our large conveyance, treatment, and distribution facilities; planning and scheduling water deliveries and power operations; and ensuring compliance with water quality, safety, and environmental regulations. I’ve been in this role for almost 2 years; I previously served in different positions within operations, primarily in the area of water quality. Before coming to Metropolitan, I worked for several years for a flood control agency as well as in the environmental consulting field.
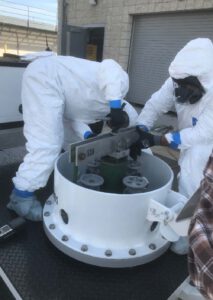
Municipal Water Leader: What are the primary areas of safety concern for a municipal water agency like Metropolitan?
Dan Guillory: Our number 1 concern is keeping our employees safe and healthy. We want to ensure that our employees go home as healthy as when they show up to work. We operate a large and complex water system, and our employees can be exposed to a variety of hazards as part of their work in the field. They use chemicals to treat water, work with high-voltage equipment, work in confined spaces like pipelines and tunnels, use cranes, do a lot of welding, and work at heights. There are also ergonomic issues, both in the field and in the office. For each of these hazards, we take a number of steps to mitigate risk. We develop training programs, procedures, and safety talks. The most important thing is to have frequent and open communication between management and employees on how to do the job safely.
Municipal Water Leader: What sorts of regulations and laws govern those safety programs?
Dan Guillory: We’re under the regulations of the Occupational Safety and Health Administration (OSHA) on the federal level and the Division of Occupational Safety and Health (known as Cal/OSHA) on the state level. We also work with local fire departments. They come out and conduct fire/life safety inspections to ensure that our facilities conform with fire code requirements for sprinklers, signage, and hazardous chemical storage and that other appropriate systems are in place. Cal/OSHA also visits our facilities and conducts structured inspections. We have an excellent working relationship with these agencies and always make an effort to keep them informed. Some employers may not welcome inspections, but we do. We have well-maintained facilities, and we’re open about the types of programs we have in place. If there are issues that need to be addressed, we always work with the regulators to make sure that they’re involved and that issues are fully resolved. We also make sure that our employees are involved. They’re aware of any regulatory inspections that are going on and are given the opportunity to speak with inspectors about any issues of concern.
Mickey Chaudhuri: We also have a regular schedule of emergency exercises that cover scenarios like earthquakes and chemical releases. Some of these are internal exercises, and some involve outside regulatory agencies. We had a large exercise last year at one of our treatment plants with first responders from the Riverside County area, including the sheriff’s department, the fire department, the public health department, and several other local government bodies. These exercises allow outside agencies and regulators to be familiar with Metropolitan’s facilities and processes. We do quite a bit of coordination to make sure that we have strong communication both internally and with external regulators to ensure a safe, coordinated response in the case of an emergency.
Municipal Water Leader: In what ways are you able to proactively deal with and reduce safety risks on the job for your employees?
Dan Guillory: We have a strong understanding of the regulations and how they apply to Metropolitan. We develop procedures to ensure that each individual within the organization—including employees, managers, and executive leadership—complies with those regulations and understands their roles. We often go beyond what the regulations require to ensure that our employees stay safe and healthy.
Another big part of what we do is planning. We’ve produced a job safety hazard checklist that we use to prepare for any project in the field. It helps alert our staff to the procedures they need to follow, the safety talks they need to have, the requirements they need to comply with, and the necessary safety and environmental permits. There’s also a process to verify that the employees doing the work have the proper training and personal protective equipment (PPE) for the job. If there are any gaps, we identify and address them prior to the work. There are things that may come up as the work progresses or under different conditions. For example, there are different hazards associated with day shifts and night shifts. We also look at what monitoring may be needed, such as monitoring air quality for work in a pipeline or structure. All of that needs to be taken into consideration when planning the work.
After a large job or maintenance activity, we also look at what went well and what could have been improved. We’re always looking at how we can do our work more safely. Even if there were no injuries, everything went well, and everyone is satisfied, we still look to see if there are ways in which we can improve things next time.
Municipal Water Leader: In what ways has technology changed the safety risks that employees deal with?
Dan Guillory: Overall, it has changed them for the better. We implemented a new computerized program a few years ago to track our injuries and work-related illnesses. This database, which records the particular circumstances of those injuries, drives us to investigate root causes and helps us see trends. Sometimes that leads to a detailed investigation, and sometimes it’s something relatively simple, but the key thing is that we want to find out the cause of the injury and learn how we can prevent something similar from happening in the future. These lessons are used to help us develop new training programs and guidelines.
For example, we had a situation a couple of years ago in which some employees in our welding and grinding operations were experiencing minor eye irritation despite using face shields, which concerned us. After some research, we began using goggles with foam inserts that completely eliminated the possibility of sparks reaching the eyes and causing any eye injuries.
The technology and equipment that is available to monitor and control field environments has also improved. There is better equipment to monitor the air flow and oxygen content in a pipeline, for instance. The PPE that is now available is also much better.
This is also true in water quality and environmental analysis. We have better analytical data and can analyze constituents down to a much lower level of concentration, meaning that we have a better idea of what employees are being exposed to and can implement better personal protective controls. Technology has definitely played a big role in improving worker safety.
Mickey Chaudhuri: Technology and innovation have also improved the way that we approach some of our capital improvements in terms of safety. It is sometimes necessary to shut down a facility or a stretch of pipeline and send individuals in for inspections, which of course takes time, complicates water deliveries, and has workplace hazards associated with it. However, there are new technologies and sensors that can detect abnormalities, leaks, and structural issues while the pipelines are still in service. These technologies help from a safety standpoint because they eliminate the need for a large shutdown and the necessity of sending people into the pipeline.
We also have an extensive preventive maintenance program for our infrastructure. We do certain inspections on a regular basis, but now many of these inspections are done through condition-based maintenance. We use data analytics to determine risk and to decide when these maintenance activities should be performed. That all helps to prevent failures and mitigate risks. I compare it to going to the doctor for your regular checkup. You’re checking in to see how you’re doing without waiting for a problem to arise. These well-planned, proactive maintenance measures using new technologies help to minimize the potential for system failures that could lead to unsafe working conditions.
Municipal Water Leader: What kinds of safety training does Metropolitan provide to its employees?
Dan Guillory: Each year, we offer over 800 classes covering nearly 100 different safety topics, including injury and illness prevention, PPE, hazard communication, hearing conservation, respiratory protection, fall prevention, high-voltage electrical safety, and confined spaces. We also have done a lot of ergonomic evaluations for our employees, both for those who work in an office environment and for those out in the field. Another training program that we always do refreshers on at this time of year is heat stress and illness prevention. We’ve always had some on-demand online classes, but about 60 percent of our classes are usually held in the classroom. As a result of the COVID‑19 pandemic, nearly all these classes have been moved online. It’s critical that employees be able to take these classes to keep their skills and certifications active. The recent transition to more online classes will have a lasting benefit for Metropolitan.
Municipal Water Leader: How do you encourage buy-in to your safety programs among employees?
Dan Guillory: We have 15 employee-run safety committees throughout the agency, located at all our major facilities. We promote employee participation in safety committees, and our employee unions are also represented. The safety committees serve a key role in reviewing safety suggestions and working with management to make sure that sound suggestions are implemented. We also have a labor-management safety committee, involving union representatives, that meets regularly to discuss issues of concern.
To provide another reminder that safety is the top priority, at many of our meetings, including our weekly operations planning meeting, a manager does a short presentation, called a safety moment, addressing a particular safety concern.
We have at least two environmental health and safety professionals stationed at each of our major facilities. They work closely with employees on issues of safety concern on a day-to-day basis. We also have a confidential hotline that any employee can use to report safety concerns. We haven’t had a call on the hotline for a couple of years, I believe because employees feel comfortable raising safety issues with their managers and others and are confident that they will be addressed in a timely manner. We make a lot of safety information readily available to employees on our internal website, including information on our procedures, training, and safety talks.
We also give an award each year to the facility that has the best safety performance and acknowledge it annually at our all-managers meeting. The criteria that decide the winner include the percentage of our training courses that the employees have completed, the number of reported injuries, the number of completed safety inspections, and the number of times that a facility has gone through the hazard checklist that we use for planning jobs. It’s competitive, and the facilities that earn this award are quite proud of it.
Mickey Chaudhuri: Dan and his staff do a great job maintaining our employees’ enthusiasm and motivation when it comes to safety issues. We don’t look at safety as an audit function that is done after the fact; it’s integrated into our operations. That is why establishing that employee buy-in is so important and provides a foundation for a successful program.
When an incident does occur in the field, sometimes involving a safety issue or a near miss, we convene a committee of independent members from multiple groups within Metropolitan to thoroughly review it and provide recommendations on how we can improve moving forward. That’s been a really valuable process. Those reports are then posted so that anybody within Metropolitan can access and learn from them.
Municipal Water Leader: What is your vision for the future of safety and risk management at Metropolitan?
Dan Guillory: Our goal is zero injuries. That’s something that we are always working toward. As part that, we have a number of different metrics. We do a good job of reporting injuries, but one metric we’re looking at improving is our reporting of near misses. These are incidents that did not result in employee injury but could have. We want to make sure they are reported so that we can address those situations and introduce corrective measures to make sure that injuries don’t occur in the future.
We also work closely with our engineering design group and review plans and specifications to make sure that they incorporate safety considerations. They do a really good job of that, but having a second review can help to identify different ways that designs can be modified to make them more ergonomic or easier to maintain.
Our labor-management committee plays an important role in strengthening our safety program by bringing issues to our attention. One recent improvement that came out of that process started with a concern an employee had about towing. We have a lot of pumps, compressors, and other equipment that we tow from one facility to another or to a job site. There were concerns about whether the vehicles that were being used for towing were appropriate for that function. In response, we came up with a system to label trucks and their hitches with their total capacity so that employees can easily verify that a particular vehicle is appropriate for a specific job.
We are also involved in professional organizations in which we network with other companies and organizations regarding safety. It is especially useful to be involved in those organizations during the COVID‑19 pandemic. We are hearing about what others are dealing with, lessons they have learned, and their experiences implementing response programs.
Mickey Chaudhuri: As a very large utility, we have billions of dollars’ worth of infrastructure assets, but we’ve always been well aware that our most valuable assets are our employees. Because of that, we take our safety program seriously. With the size and complexity of our facilities and infrastructure, we recognize that hazards are present, and we strive to be proactive in dealing with these risks. Each and every employee is responsible for safety, and transparent communication on safety issues is critical. All of that helps to build trust and foster a culture of safety within the organization.
Mickey Chaudhuri is the assistant chief of operations at the Metropolitan Water District of Southern California. He can be contacted at mchaudhuri@mwdh2o.com.
Dan Guillory is Metropolitan’s section manager for operational safety and regulatory services. He can be contacted at dguillory@mwdh2o.com.